Inside the Somerville Facility That’s Decontaminated 100,000 Masks
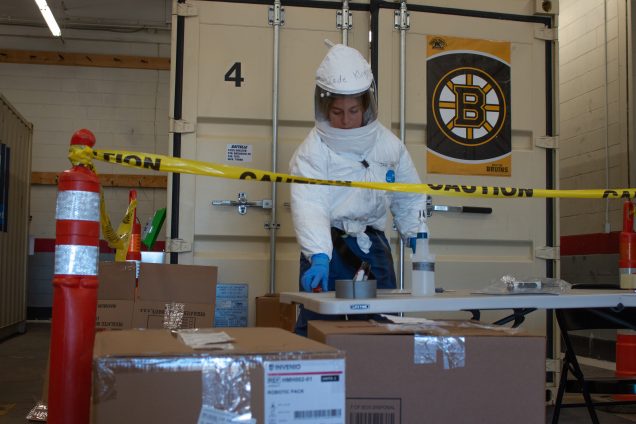
Inside the Somerville Facility That’s Decontaminated 100,000 Masks
by Caitlin Faulds
A mask decontamination facility based in the loading bay of an old Kmart in Somerville’s Assembly Row has cleaned more than 100,000 masks for reuse since mid-April, according to facility operator Battelle Memorial Institute.
The Critical Care Decontamination System facility, run by Battelle in partnership with the City of Somerville and Partners Healthcare, was the fourth N95 mask decontamination facility to be built in the US and is the second busiest nationwide, says President of Contract Research Matthew Vaughan.
“It’s just been an amazing journey,” Vaughan says.
On March 29th, in response to a nationwide shortage of personal protective equipment, or PPE, the FDA handed down approval for the Ohio-based nonprofit to develop a network of mask decontamination sites in coronavirus hotspots, Vaughan says. Each one has the ability to decontaminate more than 80,000 medical-grade masks each day.
“We’d all want everyone to have a new N95 every day,” he says. “The next best thing to that is one that has been decontaminated with a proven, scientifically validated process.”
Now, Vaughan says there are more than 40 CCDS facilities across the country, with more expected as the pandemic spreads.
“I have no crystal ball and I don’t think any of us know what will come next,” Vaughan says. “But what we do know is that these systems provide a buffer for that N95 supply chain.”
Site Lead Jonathan Coyle says it’s been no small task to get these sites up and running. He helped develop facilities in Stony Brook, N.Y. and Tacoma, Wash. before stepping in at the Boston-area site at the beginning of May.
“This is definitely by far the best one in my opinion,” he says, “not biased at all or anything.”
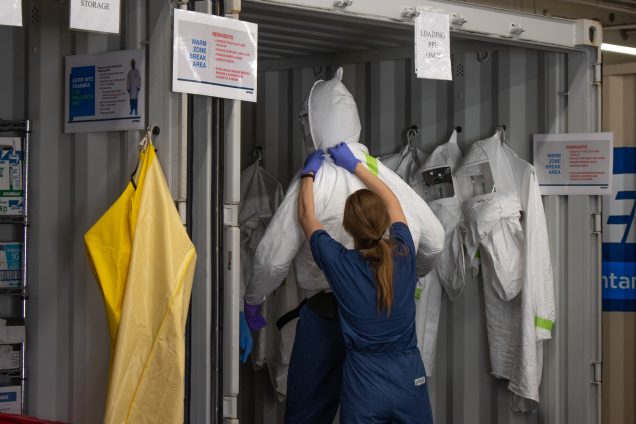
Every site is different – some indoors, some outside – but Coyle says they’re typically made up of about eight chambers, four for storage and four used as decontamination chambers. Here in the Somerville facility, due to the size of the room, there are just three chambers used for storage.
“This is the only real layout that worked for this footprint,” he says.
Inside the decontamination chambers – hung with Bruins, Red Sox, Patriots and Celtics banners in a statement of Boston pride – Coyle says staff members in biohazard suits called PAPRs, or powered air purifying respirators, arrange thousands of used masks. Then, he says vapor phase hydrogen peroxide is pumped through the chamber for several hours until it reaches a concentration known to eliminate any traces of coronavirus or other contaminants.
“From there, we then start the aeration process,” Coyle says. “So just as we pumped all that hydrogen peroxide in, we now need to pump that out. That’s usually our longest phase right now, it’s kind of where our bottleneck is.”
When all VPHP is removed, Coyle says the staff heads back in with clean PAPRs to sort the masks by five-digit identification number and box them up for couriers to return to their original location – one of 480 collection points including hospitals, clinics and fire and police departments.
All the masks go back to the same individual, according to Battelle, helping to ensure continued mask fit and lessen the user’s risk of COVID-19 infection. When they’ve been used again, the masks will come back through the facility – decontaminated and reused up to 20 times, according to Battelle policy.
“It’s a whole process,” Coyle says. “It’s just a big loop pretty much.”
Battelle’s been working on mask decontamination projects for several decades and developed this system as part of a study completed in 2016 which considered the feasibility of reusing masks during emergency scenarios. Last month, the National Institutes of Health confirmed VPHP as the “most effective decontamination method” tested, citing its ability to remove contaminants in just ten minutes.
Back in its Ohio laboratories, Battelle is working on “quite a few” other technologies to help with the coronavirus pandemic, according to Vaughan. He says their projects include research into decontamination methods for other PPE, a collaboration with Boston-based Ginkgo Bioworks to develop large-scale diagnostic solutions and the testing of coronavirus vaccines and therapies in biosafety labs.
“It’s really gratifying to be able to have our researchers who have been toiling away in obscurity for so long have their research be able to make a real-world impact,” says Vaughan. “We wish we didn’t have to, but we’re glad that we’re here and able to do that.“