Research
[Last updated on: 3/5/2024]
Thermal Wave Sensors
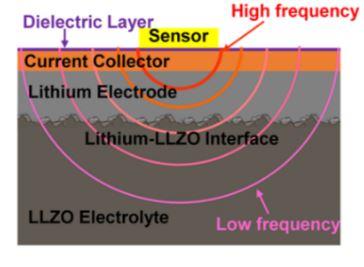
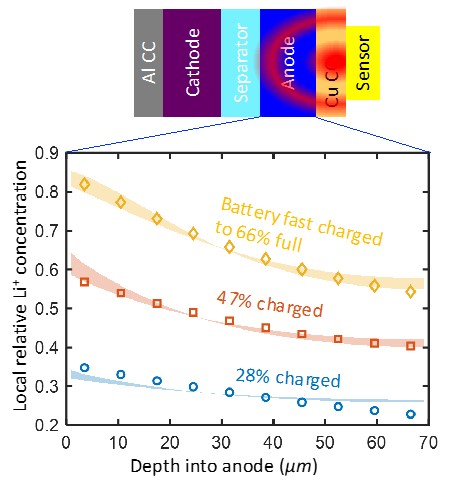
Using thermal waves, the 3ω method can noninvasively probe a sample to measure the thermal conductivity and thermal resistance of materials and interfaces under the 3ω sensor. This method can penetrate a sample up to a frequency-dependent thermal penetration depth, δp ~ √(D/2ω), where D represents the thermal diffusivity of the sample and 2ω is the thermal wave’s frequency. By varying the modulation frequency (ω), the penetration depth can be manipulated, thus allowing for a range of spatial resolution.
These sensors can be utilized on batteries to determine Lithium-ion transport at the interfaces, on fuel cells, biological samples, and a variety of other applications.
Direct Air Capture of CO2
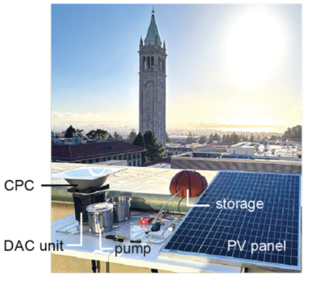
To effectively slow global warming temperatures to the desired rate set by the US Department of Energy, society must not only stop producing carbon emissions but must also actively work to remove excess CO2 from the atmosphere. This design exceeds cost standards of $100 tCO2-1 (the ‘Carbon Negative Shot’ 2030 goal), is passive (requires no human intervention), and has a high capture capacity.
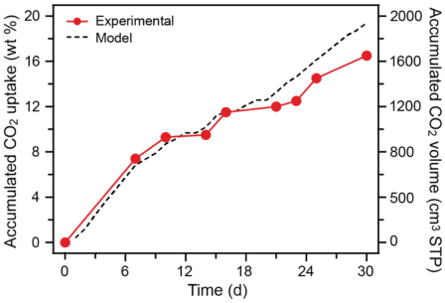
The system design, adsorbent material, and techno-economic analysis (TEA) are all active parts of our, and our collaborator’s, work. The system is powered by a PV panel, which enables the pumps to pull the air through the device. The adsorbent is a cooperative Metal-Organic Framework (MOF) with desirable capture capacities, cycling stability, and mechanical properties. The thermal properties of this material is currently unknown, and being studied by our group. Finally, the TEA allows our research team to understand how to make this system a reality in society so that we can work towards decreasing the amount of excess greenhouse gasses in our atmosphere.
High-Temperature Thermal Energy Storage
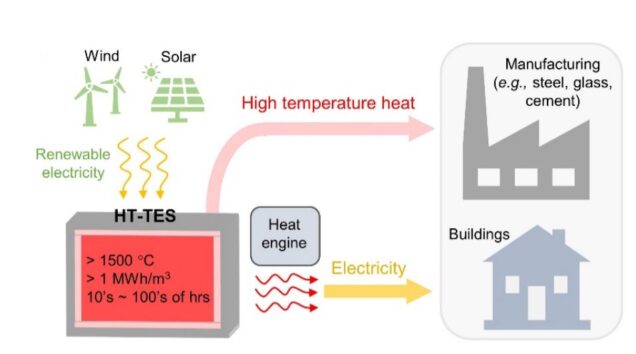
There is a large gap in providing large-scale deployable energy storage with zero-emissions. High-temperature thermal energy storage is a potential solution that is low cost, scalable, stable, and efficient. We are working to optimize the mechanical, electrical, and thermal properties a ceramic-carbon composite to make this a reality. These composites show a high energy density, high mechanical hardness, desirable electrical and thermal conductivity, and have a low cost, thus making them an ideal material to study.
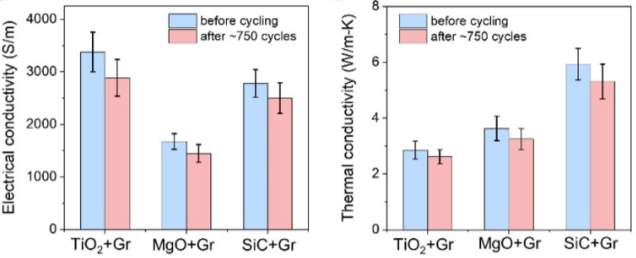
The HT-TES system is zero-emissions, powered by renewable energy sources when needed. It operates at temperatures greater than 1500 degrees C, providing high-temperature heat to industrial applications, which make up nearly 1/3 of the United State’s energy consumption. The system is able to provide greater than 1 MWh per cubic meter of the material, and can store energy for tens to hundreds of hours, thus solving the intermittency issue of currently implemented renewable energy sources. Additionally, when coupled with a heat engine, this technology can provide electricity for residential, commercial, and other applications.
Machine Learning Inverse Design of Nanomaterials

Optically designed metamaterials enable the manipulation of electromagnetic radiation and can be utilized in a variety of applications, from sensing, cloaking, and imaging. These materials allow us to control incident light and thermal emission in visible and infrared wavelengths, thus providing possible breakthroughs in energy storage, quantum computing, and dark matter detection.
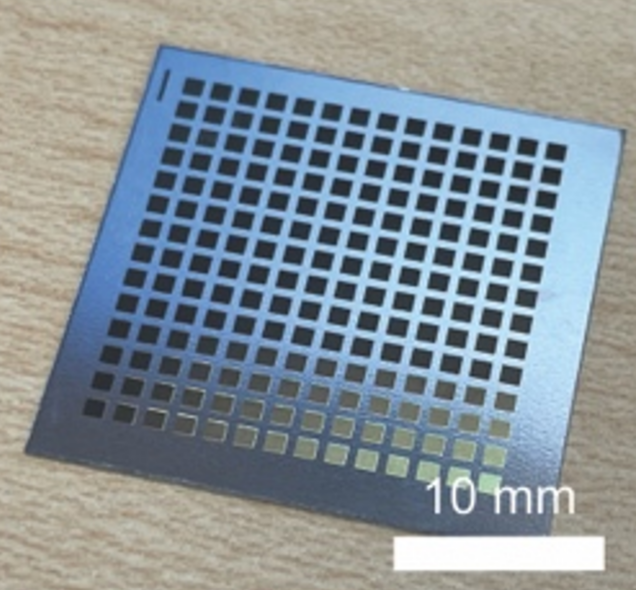
This work utilizes a femtosecond laser to design the optically fabricated materials and a Tandem Neural Network (TNN), which allows the prediction of laser parameters based on the nanofabricated surface inputs, particularly the spectral emissivity.
Over 35,000 data points have been utilized thus far to train the TNN, which has exhibited a root-mean-squared-error of less than 2.5%.